Though unaware of any specific issues relating to energy usage, the fruit processor felt that it would be good practice to identify the major users of energy in its factory, and to investigate opportunities for energy savings and efficiency improvements. The first step was to engage Smart Energy Solutions NI, an expert in energy efficiency, to inspect the production processes and, where possible, take manual readings from panel meters to provide an indication of energy usage. Discussions were also held with the factory operations manager to determine which items of equipment were likely to be the biggest energy users.
The information gathered was used to develop a real-time cloud-based solution for continuously monitoring critical circuits, so that efforts to reduce energy usage could be accurately targeted on those areas where savings were most likely to be significant. Continuous monitoring would also allow the effect of energy efficiency measures to be assessed quickly and reliably, as well as making it possible to confirm the ongoing performance of those measures’ months and even years after they had been implemented.
As a preliminary part of this exercise, Chauvin Arnoux PEL103 power and energy loggers were fitted to the plant’s main power users and, almost immediately, these produced an interesting and concerning result: the refrigeration system on the main cold store was running continuously and was consuming energy costing £650 per week at the prices then prevailing. The cold store service provider was asked to check the installation and found that it was switched to manual override, possibly as a result of some earlier problem with the control system.
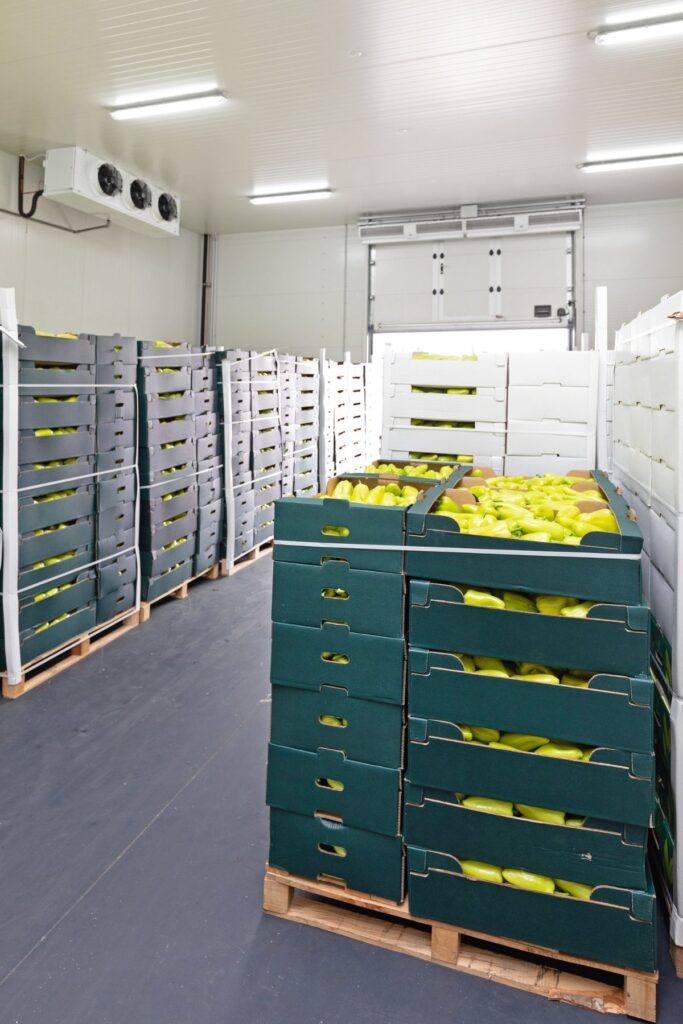